Stronger. Lighter. It’s the dichotomy that nearly all fleets chase when it comes to spec’ing new equipment. This lean, mean spec’ing strategy can boost efficiency and provide equipment longevity. When you think about suspensions for demanding applications, tried-and-true steel spring suspensions spring to mind. (Pun intended.) But what if there was another way–a suspension that provided muscled performance without the bulk of steel? That’s where composite springs come in.
Composite springs aren’t a new concept. They have been around since the late 1970s, and while they quickly found a home in automotive applications, they continue to grow in the commercial market. As the name implies, a composite spring still utilizes the typical leaf construction, but the steel spring is replaced by the composite spring that helps improve fuel economy, resist corrosion, maintain ride height and provide improved vibration and harshness feedback. Bogie Leaf Spring For Bpw

The most immediate and visible ROI bullet point is the weight reduction.
“As people think about composite springs, weight savings instantly comes to mind–and it’s true. Composite springs are typically anywhere from 50 to 60% of the weight of a comparable steel springs,” said Bryan Romer, Hendrickson Composites business unit director at Hendrickson Truck Commercial Vehicle Systems. “Along with the weight savings, composite springs offer corrosion resistance. Fleets that run their trailers in the winter time often drive through salt and road slurry–that can cause rust and damage to improperly treated steel components.”
Romer explained that general composite spring construction features millions of glass fibers that run from end-to-end on the composite spring. In the event such composite springs are exposed to road debris impacts, any potential excess wear or damage may be limited to a small number of those millions of fibers.
Further, if such wear or damage eventually develops into a visual sagging condition in the composite spring, a driver should have the ability to drive it the vehicle to a repair location to have it worked on.”
Speaking of sagging, Romer noted that certain types of steel springs also may tend to sag over time due to the nature of the material, construction, operating conditions, and other factors.
“With composite springs, we can often take a spring that has years of service in the field, bring it back into the shop, and it will fit right back into the mold that it came out of,” Romer said.
Hendrickson offers a complete line of composite spring assemblies from light- to heavy-duty applications, Class 1 to 8 trucks and trailers. For more information on composite springs, click here to visit the Hendrickson website.
Volvo Trucks places safety and sustainability at the forefront of every decision we make. It is our responsibility at Volvo Trucks to protect and preserve the finite resources of our planet. While making our business environmentally and financially sustainable, we will, together with our customers, leave a better world to our future generations.
By the time you finish reading this article, you’ll realize that ensuring optimal tire performance can be as easy as ABC.
Achieving optimal tire load capacity is a crucial balancing act that every fleet strives to master. The load on the tires directly impacts profitability, the environment and the fleet's operational efficiency. It is essential to maximize each delivery's potential while preserving tire performance, minimizing wear and prioritizing safety.
What to focus on when it comes to heavy-duty truck diesel engine coolant maintenance.
Reproductions made of cheaper, less stable materials are on the rise in the global market.
Tire pressure, or a lack thereof, can be a significant driver of overall fuel consumption. In fact, research from NACFE reveals that a 0.5-1.0% increase in fuel consumption is seen in vehicles running with tires underinflated by just 10 PSI. It is important to note the council also found about one in five trailers are
Trailer service pop quiz: Do you consider inspections “maintenance”? Answer: Maybe you should, according to Greg Dvorchak, Engineering Supervisor – Brake and Wheel-End Division, Hendrickson. “Inspection is maintenance,” says Dvorchak. From his perspective, service needs and preventive maintenance are two different things. Preventive maintenance is done to extend intervals between service or avoid unplanned wheel-end
Essential maintenance tips for heavy-duty truck slack adjusters in truck safety to ensure optimal brake performance.
The Primaax EX platform is designed for vocational, severe service and heavy-haul applications.
The common truck tire creation adage used to be: Lower rolling resistance and increased efficiency come at the cost of tire durability. Today, that adage might not hold so true.
The SuperTruck II demonstrates 16 MPG through hybridization—a 170% improvement compared to the baseline model.
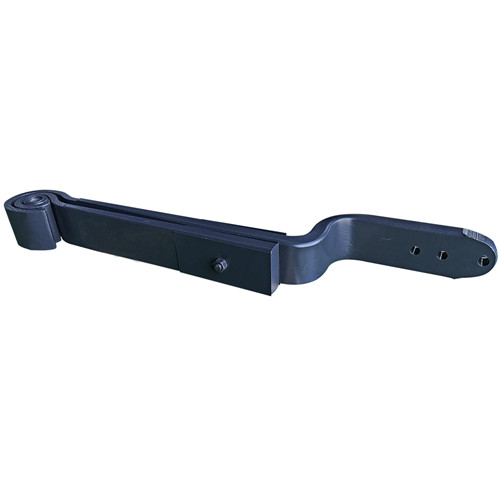
Isuzu Elf 450 Chasis 2009 Truck industry content for fleet owners and managers