The band COIN performed in Bucknell’s Gerhard Fieldhouse on Saturday, Sept. 9. COIN is based in Nashville, Tenn. and composed of members Chase Lawrence (lead singer), Joe...
This past weekend, the Bison Women’s Soccer team had two memorable home game victories versus Colorado College and Air Force. They began their weekend on Thursday, Sept.... Pa Plastic Material
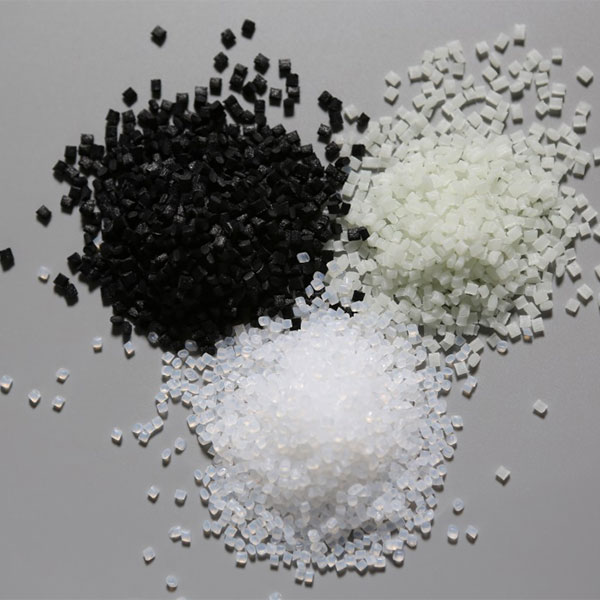
Football wins home opener vs. VMI
Bucknell Only Likes Their Lemons Lulu
The world’s leading producer of wrestling mats is Resilite Sports Products, located in Northumberland, Pa. $3.5 million of its annual sales come from its Zip Mat product, which features a polyethylene ‘Zip’ to connect the six pieces of the mat together.
However, the machine Resilite used to attach the polyethylene ‘Zip’ connector to the vinyl mat surface is recently no longer produced by its manufacturer. As a result, Resilite is now partnering with Bucknell University’s College of Engineering on a nearly $70,000 project funded by a Manufacturing PA initiative grant, to have senior engineering students help design, manufacture and commission a new machine for the process.
Jean Gilbert DeArmitt, president of Resilite Sports Products, said, “[While] partnering with Bucknell, we’re going to learn a lot. It’s an awesome opportunity to engage with the community and learn even more about our product.”
Two mechanical engineering students Joe Carey ’24 and Hunter Vestal ’24 along with Professor Craig Beal, the project’s faculty adviser, have been gathering measurements throughout the summer on both the machine and the process.
“From the student side, it’s phenomenal,” Beal says. “Students learn a lot of things in class and we hope they can solve problems and apply what they’ve learned.”
This gives Carey and Vestal the perfect task for their required Bucknell Engineering senior design project— and they are excited to do it.
“It’s crazy to know that I’m involved in something so big [$3.5 million in annual sales],” Carey says. “I’m just using the technical knowledge that I’ve gained through school to contribute to this company, so it’s really a cool experience.”
Improving the speed of the process and reducing the physical strain on the Resilite operators is the main focus of the design for the new machine.
“My role in this project is defining exactly what parameters we need to hit to make a successful machine… finding out what temperature we need to hit to get the machine to run at the speed we want in order to make it as efficient as possible,” Vestal says.
The manufacturing challenge is a perfect project for Governor Josh Shapiro’s Manufacturing PA Innovation Program, which seeks to collaborate between Pennsylvania universities and manufacturers. This Department of Community and Economic Development program awarded $2.1 million in grants to 31 projects in April. Bucknell Small Business Development Center Director Steven Stumbris and Innovation Engineering Manager Ian Proud worked with Resilite and the University on the application.
Beal says two additional senior engineering students will join Carey and Vestal on the senior design project this fall. The group will work with Resilite throughout the academic year with the goal of having a working machine by the end.
The weekly student newspaper of Bucknell University
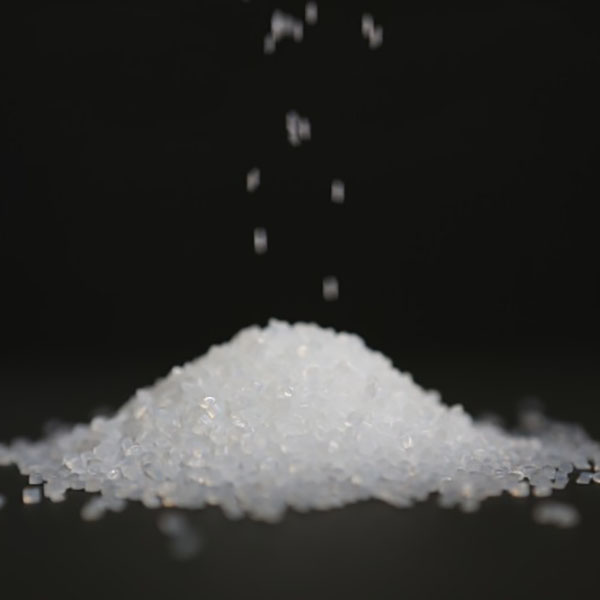
Co-Extrution Film Your email address will not be published. Required fields are marked *